Recycling Composites with Chemistry
See How Chemistry Can Bring Airplanes Back from the Dead.
February 24, 2020
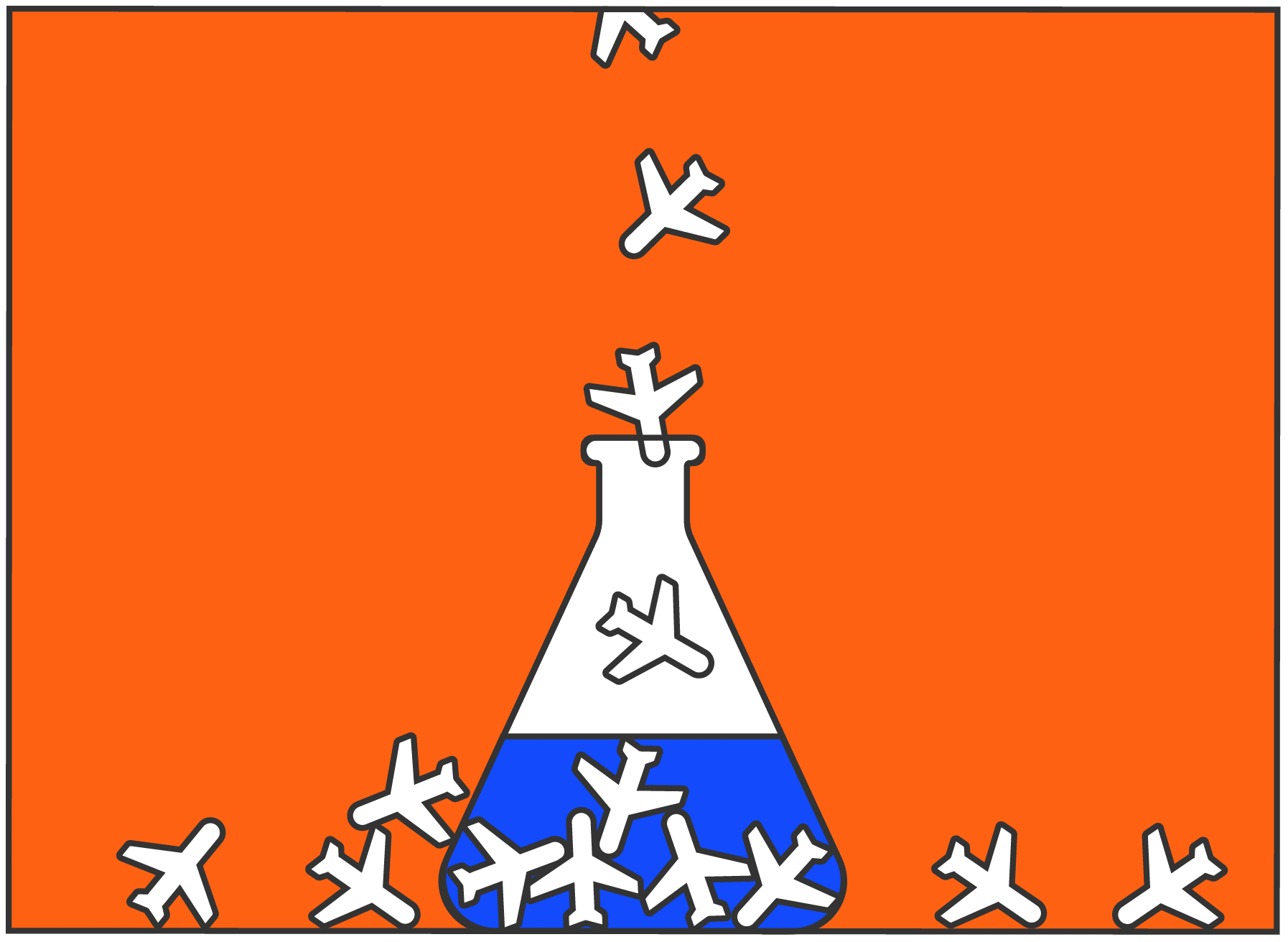
Opening Google Maps, just outside the city of Tucson, you may find this spectacular scenery where thousands of aircraft are stored in desert fields that span 2,600 acres. This place is called the 309th Aerospace Maintenance and Regeneration Group, but it is widely known for its chilling nickname, The Boneyard.

Being the largest airplane boneyard in the world, it houses over 4,000 aircraft that retired from their lifetime service awaiting dismemberment, scrapping, or simply nothing. The depressing news is that this is what happens to most retired aircrafts today. When they reach their lifespan, only less than half of the materials are taken away and recycled, leaving the rest sent to landfill.
Materials that Beat Metals
One large component of the unrecyclable parts in the aircraft is carbon fiber reinforced polymer composites (CFRP). These materials are essentially plastic reinforced by carbon fibers and they are lightweight, strong, and durable. The idea of CFRP is similar to reinforced concrete, in which the cement concrete resembles polymers, and steel bar frames reinforce it inside similar to the role of carbon fibers in CFRP.
The building block of CFRPs is the carbon fibers. They are made of thin, long carbon filaments woven together like fabrics. Then, these sheets of carbon fabrics are stacked together and infused with a polymer matrix, or put more simply, plastic resins. These polymer materials we commonly call plastics are made of large molecules with long carbon chains and often repetition of subunits. What’s more, the ingredients of CFRPs are customizable for specific applications—depending on the types of additives, the CFRP can obtain select properties such as high-temperature resistance, flexibility, or conductivity.
Over the past three decades, CFRP has gained immense popularity, especially in aerospace applications, wind turbines, and marine products. More recently, they also showed emerging potentials for large-scale demand in consumer products such as automobiles, civil engineering, and even sports equipment. This is because these composites can be formulated for specific and versatile purposes, and such flexibility, combined with the aforementioned high strength-to-weight ratio makes them a favorable choice compared to some traditional metal alloys.
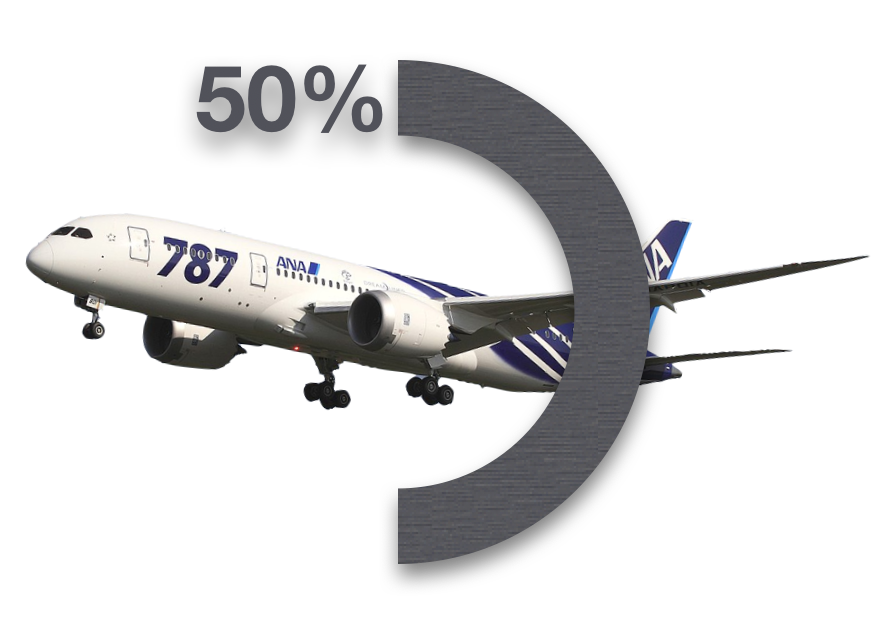
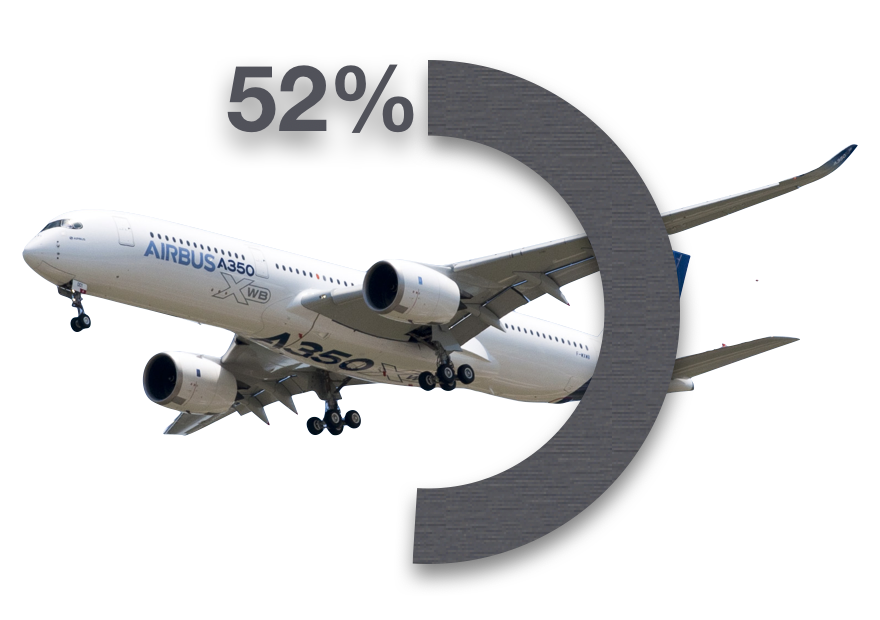

What’s the Problem?
The increasing demand results in the rising amount of waste, and the major issue with CFRPs is that there lacks an effective, robust solution to recycle them. Amplifying the problem, 10% to 30% of the starting material for manufacturing CFRP composites goes to production waste, and there is no solution for reusing the production waste. Therefore, without a mature method to complete the material lifecycle, CFRP is hindered from being put into larger-scale production and entering the consumer market, and it also fails to compete with popular metals such as aluminum and steel in the mass market, where a developed recycling system exists for them.
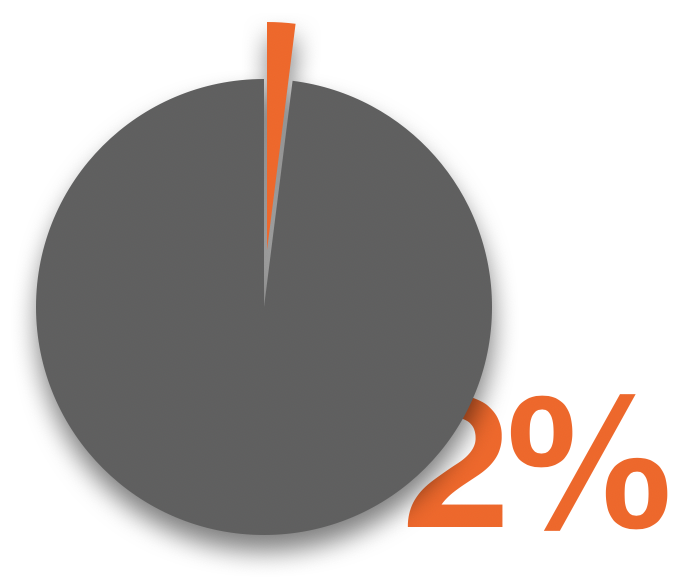
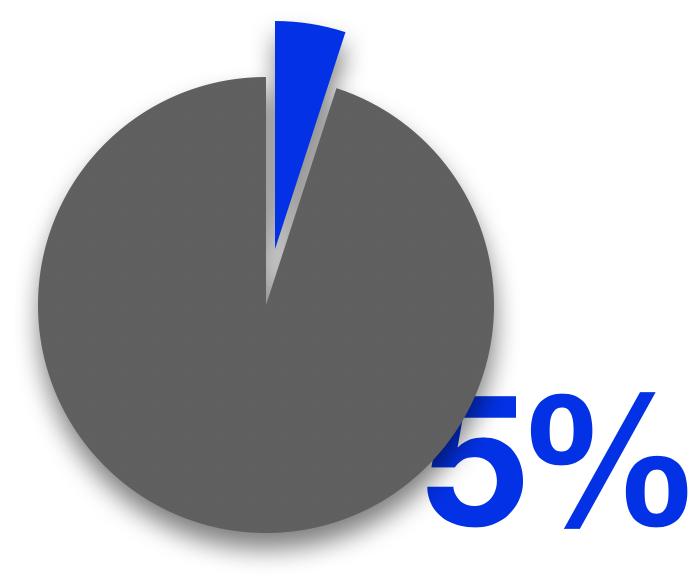
The challenges in the disposal process actually originate from the advantages of these materials. During its production, CFRP undergoes an irreversible reaction called curing, in which the solid polymer gradually hardens from originally viscous liquid resin under heat. The curing process induces the polymers to cross-link and leads to a permanent physical change from a malleable state to the final stable product. To resolve the recycling problem of CFRP, we need to figure out how to reverse this chemical process. As a result, solving CFRP sustainability essentially becomes a pure chemistry problem.
The chief goal in recycling CFRP materials is to close the loop of recycling and reusing the materials. Specifically, we want to break down the polymer to smaller reusable molecules while preserving the length of the carbon fibers so they are in reusable condition, and the separated materials can then be used for manufacturing new composites.
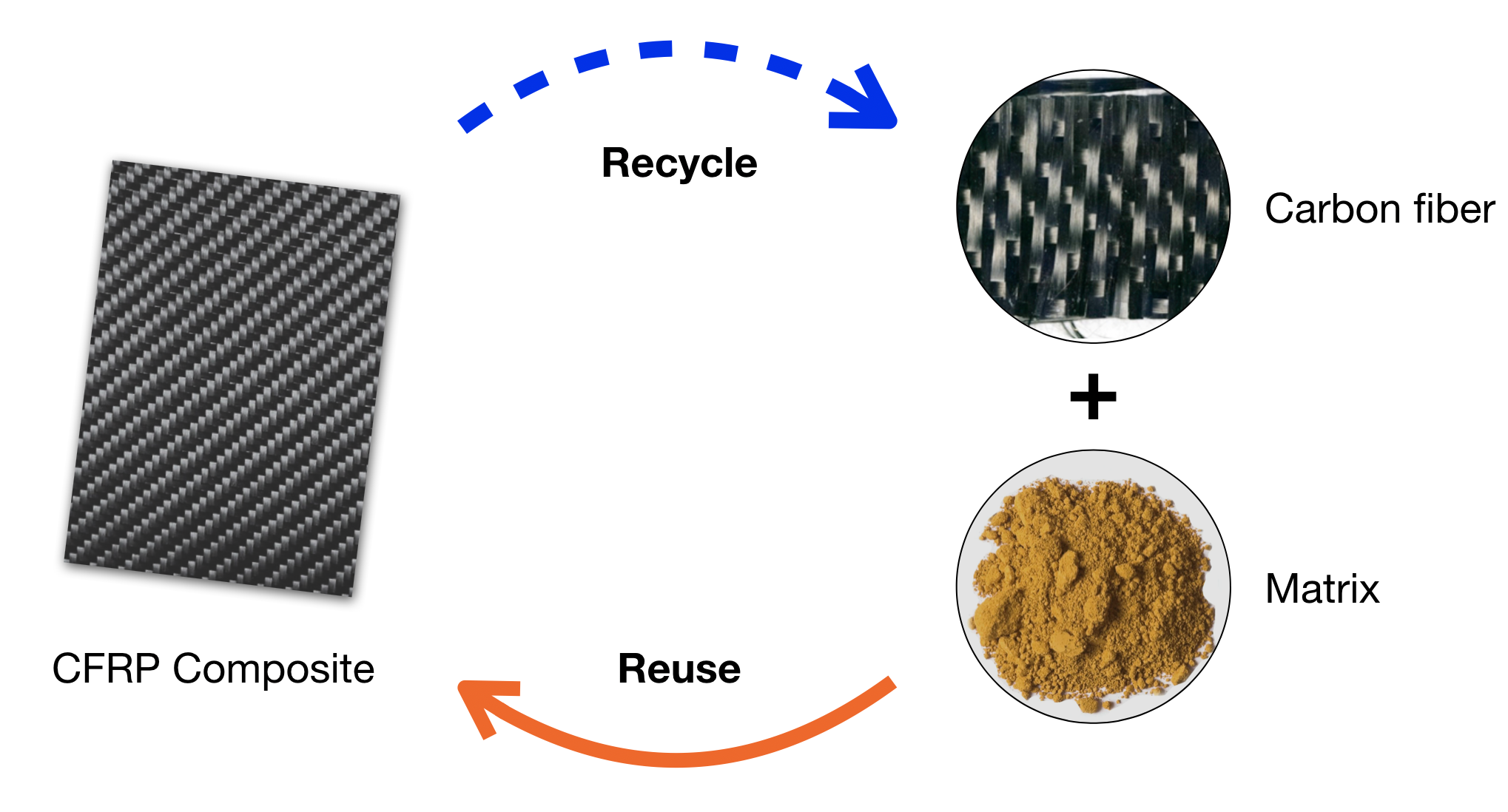
The innovation also needs to be sustainable and environmentally friendly. The existing ways to recycle CFRP are far from ideal due to the many negative impacts. Pyrolysis, the current decomposition technique for composites, involves high temperature, pressurized environment, and hazardous reagents. These reaction conditions not only cause safety and health hazards but, more importantly, also put the environment at stake. The carbon fibers are also destroyed in the process and consequently drastically diminished in strength and value.
What Are We Working on?
At the University of Southern California, Travis Williams research group in Loker Hydrocarbon Research Institute partners with the Steve Nutt group in M. C. Gill Composites Center. This collaboration offers expertise that spans across chemistry and engineering, aiming to develop a sustainable, applied technology that tackles the composite recycling problem. Since I work with professor Williams, our group focuses on the chemical recycling of the composites. In order to address the issue of sustainably recovering materials from composites, we start by looking at what reagents will work and how they can work within the composite’s solid structure. Therefore, we are currently working on methods that use catalysts to break down the commonly-used polymers used in these composites into smaller fragments. Based on that, in the long run, the goal remains to apply these catalytic methods to disassemble the CFRP matrix with sustainable reagents and mild conditions to retrieve useful small molecules and retain the length of carbon fibers.

At the beginning stage of the research, we discovered that oxidative catalysis is the key to achieve the long-term goal. What is oxidative catalysis? Think of oxidation* as inserting an oxygen atom to interact with a weak, reactive point of the polymer molecule, and with the help of catalysts, we can speed up the reaction. In our case, we use oxygen-containing reagents to react with that weak spot, and eventually break the connection to two separate terminals, achieving depolymerization.
* Side note: read this for a more rigorous definition of oxidation.
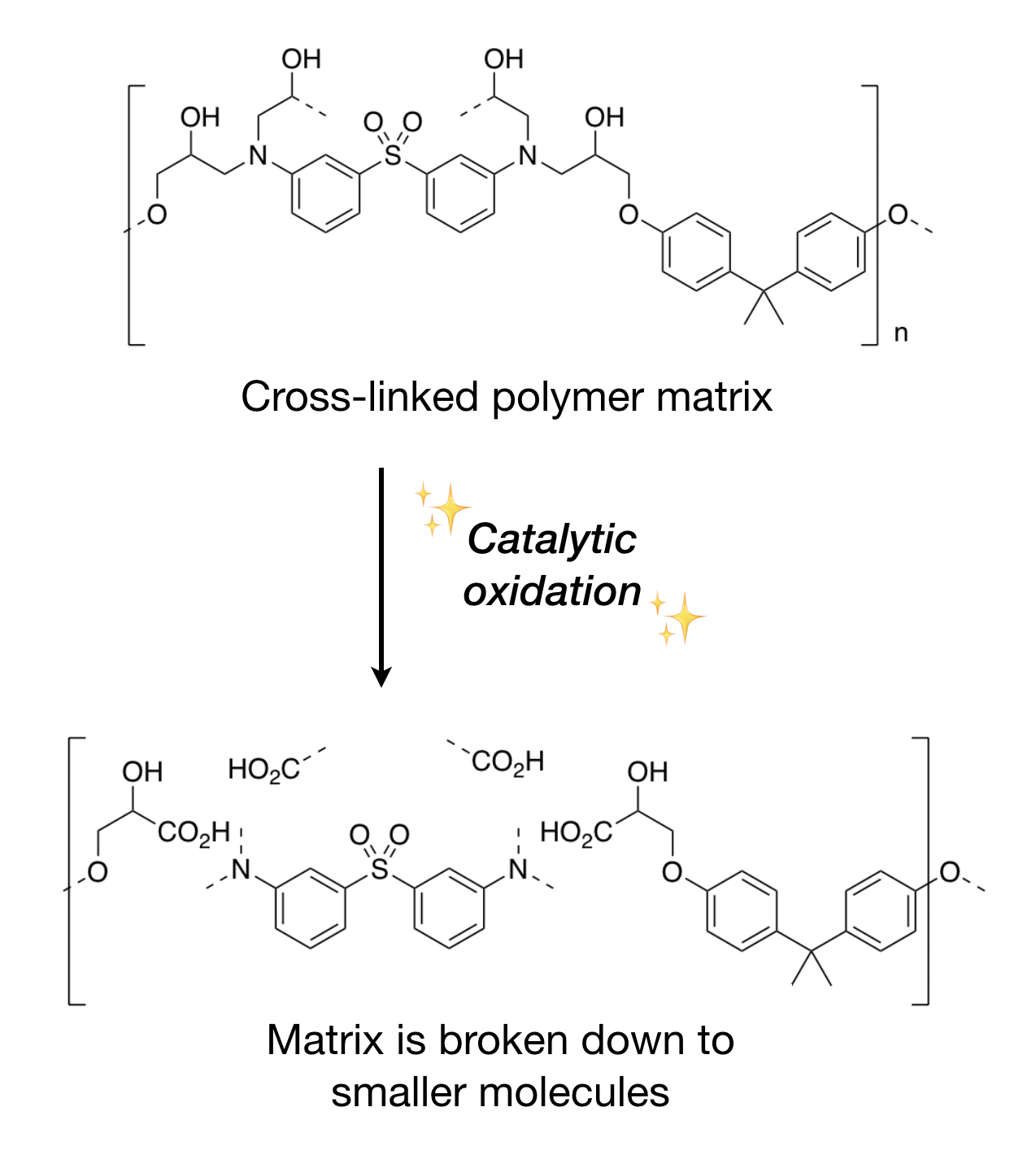
So far, we are focusing on a common type of polymer used in CFRPs named amine-based epoxy, which is described by its starting material molecules. Previously, we have succeeded in decomposing these polymers while separating carbon fibers using acidic hydrogen peroxide (H2O2) solution as a source for oxidation. However, it cannot be developed for large-scale usage due to two issues. Firstly, as we know, H2O2 is a reactive and corrosive material, and another fun fact is that it is an explosive in high concentrations and an expensive reagent. Therefore, it is a huge safety hazard and financial burden to use H2O2 in large quantities. Secondly, it destroys the polymer molecules to fragments that have no value in reuse, again proving it is not a sustainable option.
However, experimenting with H2O2 helped us to map out the mechanism of how oxygen atom interacts with the polymer. When an oxidizing agent is introduced to the molecule, it undergoes a process called oxygen atom transfer (OAT) followed by elimination. The oxygen atom would form a bond with the targeted spot in the molecule. After some transfers of electrons between the neighboring bonds, the oxygen is eliminated, leaving the target spot with a much weaker connection that can be readily cleaved apart.
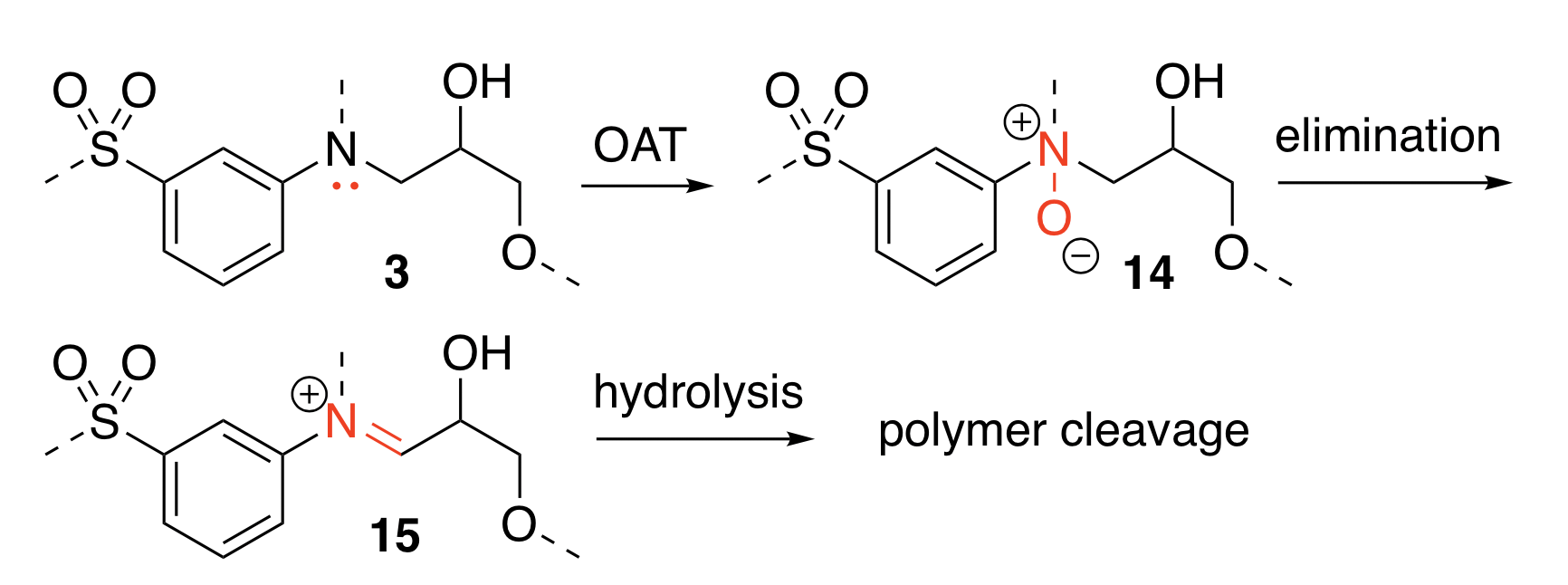
With the understanding of how the reaction works, we just need to find alternative reagents that play equivalent roles in the mechanism. Recently, we started experimenting with oxygen gas (O2) as the oxidizing agent and pairing it with a variety of catalysts that helps to deliver the oxygen atom from O2 to the targeted spot on the polymer. We have seen some promising results of polymer cleavage under moderate temperature and atmospheric pressure, suggesting that we are one step closer to reaching the goals.
It would be cheering news to realize this technology and apply it in real life. The potentials of CFRPs are not to be underestimated, and the fruition of such technology can immensely benefit our lives and the environment by introducing this wonderful new material to the mass market. I am excited about this research as it demonstrates how the work chemists are doing is closely relevant and has powerful implications in the world. After all, how cool is it that chemistry can (in a way) bring airplanes back from the dead!
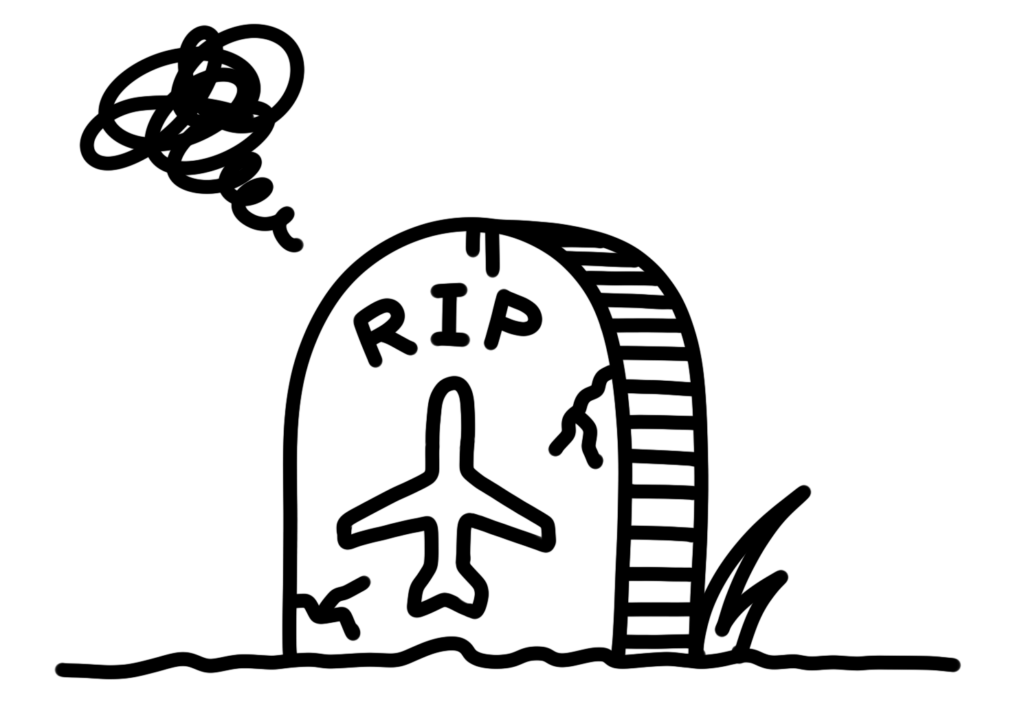
Relevant paper:
Navarro, C.A., Kedzie, E.A., Ma, Y. et al. Mechanism and Catalysis of Oxidative Degradation of Fiber-Reinforced Epoxy Composites. Top Catal 61, 704–709 (2018).